Unbelievable Tips About What Is The Range Of A Torque Sensor
-1024x651.png)
Understanding the Range of a Torque Sensor
1. Defining the Torque Sensor's Operational Boundaries
So, you're curious about the range of a torque sensor, huh? Well, buckle up, because we're about to dive into a world of twists and turns (pun intended!). The "range" of a torque sensor, at its core, refers to the spectrum of torque values it can accurately measure. Think of it like a ruler; it can only measure lengths within its marked graduations. A torque sensor works similarly, but instead of inches or centimeters, it deals with Newton-meters (Nm) or pound-feet (lb-ft).
But it's not quite as simple as just looking at a number on the sensor's datasheet. A sensor might technically be able to read from, say, 0 to 100 Nm. However, that doesnt mean it's accurate across that entire range. Accuracy is a whole different ballgame, and we'll get to that. The key takeaway here is that the range defines the potential measurement capability, but understanding its practical application requires considering accuracy, linearity, and a few other sneaky little variables.
Why is this "range" thing even important? Imagine using a tiny kitchen scale to weigh an elephant. Its just not going to work! Similarly, if you're trying to measure the torque generated by a massive industrial motor with a sensor designed for delicate laboratory experiments, you're going to be sorely disappointed (and possibly break something expensive). Choosing the right range ensures you're operating within the sensors designed capabilities, leading to reliable and meaningful data.
Furthermore, selecting the appropriate range can significantly affect the overall system performance. A sensor with a range far exceeding the expected torque values might be less sensitive, leading to lower resolution and less accurate readings in the relevant portion of your measurement. Conversely, a sensor with a range that is too narrow risks overload and potential damage, not to mention giving you useless, maxed-out readings.
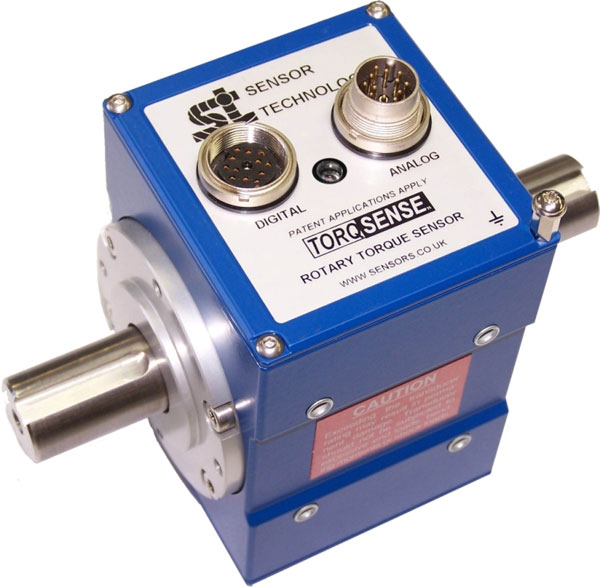
Digging Deeper
2. Beyond the Datasheet
Alright, let's peel back another layer. While the manufacturer's specifications give you a starting point, several factors can impact the usable range of a torque sensor in a real-world scenario. Temperature, for instance, is a notorious troublemaker. As temperature fluctuates, the sensor's materials expand and contract, potentially affecting its calibration and accuracy. This effect, naturally, will alter the sensor's response over the stated range.
Then there's the issue of linearity. A perfectly linear sensor would produce an output signal directly proportional to the applied torque across its entire range. In reality, though, sensors tend to exhibit some degree of non-linearity, especially at the extreme ends of their range. That means that the readings might be less accurate at very low or very high torque values, effectively shrinking the usable range where reliable measurements can be obtained.
Electrical noise is another culprit. Environmental electrical noise can interfere with the sensor's signal, making it difficult to discern the true torque value, particularly when measuring small torques. Proper shielding and signal filtering can mitigate this, but it's a factor to consider when determining the practical lower limit of the sensor's range. Think of it like trying to hear a whisper at a rock concert you might technically be able to hear something, but distinguishing it from the background noise is a challenge.
Finally, consider the sensor's mounting and application. A poorly mounted sensor, subject to vibrations or misalignment, will undoubtedly produce inaccurate readings. Similarly, if the sensor is exposed to harsh environments (corrosive chemicals, excessive dust, etc.), its performance and lifespan will be compromised. So, ensuring proper installation and environmental protection is crucial for maximizing the usable range and maintaining long-term reliability.

What Is A Dual Range Torque Sensor? Features And Benefits Of 4503B
Accuracy vs. Range
3. Precision Matters
Let's talk accuracy. It's a close relative of range but plays by different rules. Accuracy defines how close the sensor's reading is to the true torque value. A sensor might have a broad range, but if it's wildly inaccurate, that range is essentially useless. Think of it like a clock that runs fast; it can display any time of day (broad range), but it's never actually correct (poor accuracy). Therefore, understanding accuracy within the specified range is key to getting dependable data.
Accuracy is often expressed as a percentage of the full-scale range (FSR) or as a percentage of the reading. FSR accuracy means that the error is a percentage of the sensor's maximum capacity. Percentage of reading accuracy means the error is proportional to the measured value. So, a sensor with 1% FSR accuracy on a 100 Nm range could be off by as much as 1 Nm at any point within that range. A 1% reading accuracy means the error is 1% of the value you read; better for higher-torque measurements.
Why does this matter? Imagine you're using a torque sensor to tighten bolts on a critical aircraft component. If your sensor is inaccurate, you might under-tighten the bolts, risking structural failure, or over-tighten them, potentially damaging the threads. In such scenarios, even a small error can have catastrophic consequences. Therefore, selecting a sensor with sufficient accuracy for your specific application is paramount to ensuring safety and reliability.
Also, remember to consider the combined effect of range and accuracy. A sensor with a very wide range but poor accuracy might be suitable for applications where only a rough estimate of torque is needed. However, for precise measurements, a sensor with a narrower range and higher accuracy will generally be the better choice. It's all about finding the right balance between these two parameters to meet the specific requirements of your application.

Measuring The Force Of Rotation Torque Sensors Technical Articles
Calibration and Maintenance
4. Ensuring Long-Term Reliability and Accuracy
Even the best torque sensor will drift out of calibration over time. This drift is caused by various factors, including wear and tear, temperature fluctuations, and environmental exposure. Regular calibration ensures that the sensor continues to provide accurate readings throughout its lifespan. It's like taking your car in for a tune-up; it keeps everything running smoothly and prevents unexpected breakdowns.
Calibration typically involves comparing the sensor's output to a known torque standard and adjusting the sensor's internal settings to minimize any discrepancies. The frequency of calibration depends on the sensor's application, operating environment, and the required level of accuracy. For critical applications, calibration might be necessary every few months, while less demanding applications might only require annual calibration.
Besides calibration, proper maintenance is also essential for maintaining the sensor's accuracy and extending its lifespan. This includes regularly cleaning the sensor, inspecting for any signs of damage, and ensuring that the wiring and connections are secure. Also, avoid exposing the sensor to conditions outside of its specified operating range, such as excessive temperature, humidity, or vibration.
Neglecting calibration and maintenance can lead to inaccurate readings, reduced sensor lifespan, and potentially costly errors. Think of it like ignoring a small leak in your roof; it might not seem like a big deal at first, but it can eventually lead to significant water damage. Similarly, neglecting your torque sensor can result in inaccurate data that compromises the integrity of your application.
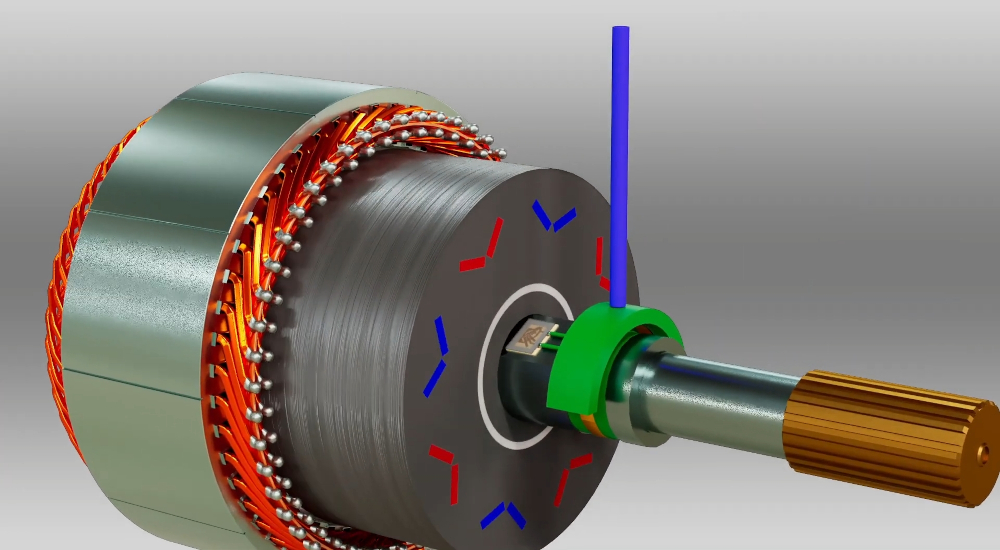
Torque Sensing EMobility Engineering
Choosing the Right Torque Sensor Range
5. Matching the Sensor to the Task
In summary, selecting the appropriate range for a torque sensor involves more than just glancing at the manufacturer's specifications. It requires careful consideration of the expected torque values, the required accuracy, the operating environment, and the application's specific requirements. Always choose a sensor range that comfortably encompasses the expected torque values, but avoid oversizing it unnecessarily, as this can reduce sensitivity and accuracy.
Remember to factor in potential variations in torque, such as peak loads or transient events. It's always better to have a little headroom to prevent overloading the sensor. Also, consider the impact of temperature, linearity, and electrical noise on the usable range. These factors can effectively shrink the range where reliable measurements can be obtained. Selecting the right range is all about optimizing the sensor's performance for your specific application.
Don't underestimate the importance of calibration and maintenance. Regular calibration ensures that the sensor continues to provide accurate readings throughout its lifespan, while proper maintenance prevents damage and extends its operational life. By following these guidelines, you can ensure that your torque sensor operates within its optimal range and delivers reliable, accurate data for years to come.
Ultimately, the best approach is to consult with a torque sensor expert who can help you select the appropriate sensor for your specific needs. They can provide valuable insights and guidance, ensuring that you choose a sensor that meets your requirements and provides reliable performance. So, don't hesitate to reach out for professional assistance; it can save you time, money, and potential headaches in the long run.
